Rail welding is an important aspect of crane operation and maintenance, as it ensures the safety and stability of the crane's movement along its tracks. When done properly, welding can significantly improve the durability and longevity of the crane's rail system. Here are some positive aspects of rail welding for cranes.
Firstly, rail welding ensures a smooth and uninterrupted movement for the overhead crane, as gaps or misalignments in the rails can cause the crane to shake or derail. Welding creates a strong and continuous joint between rail sections, ensuring that the tracks are level and aligned properly. This improves the crane's movement efficiency and reduces the risk of accidents or damage to the crane.
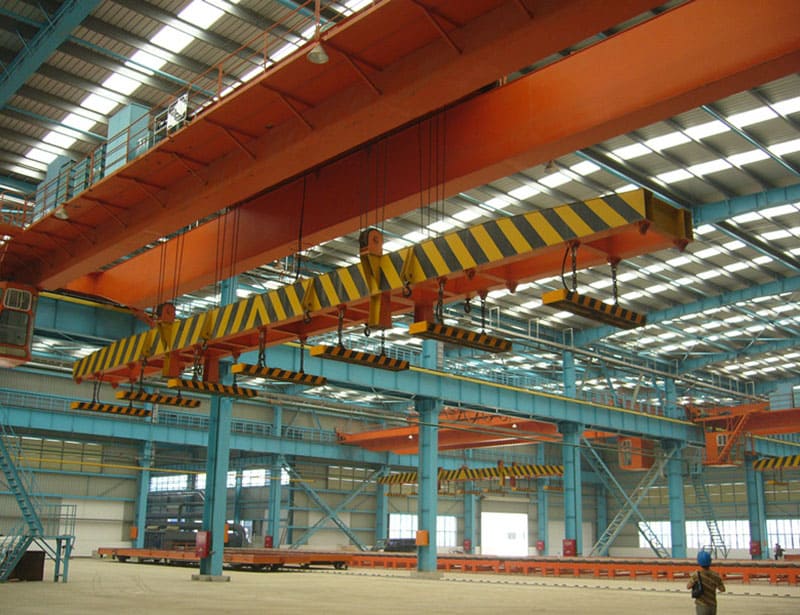
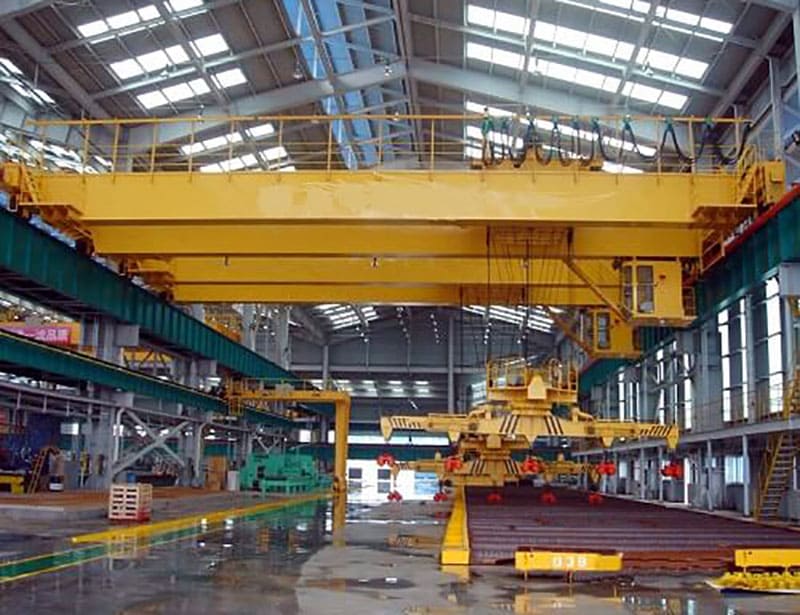
Secondly, rail welding reinforces the rail system's durability and resistance to wear and tear. Welding ensures that the rails can withstand heavier loads and stresses without breaking or bending, increasing their lifespan and reducing the need for constant maintenance or upgrades. This also helps to reduce downtime for the crane, as it can continue to operate without interruptions due to rail defects.
Thirdly, rail welding can enhance the safety and reliability of the gantry crane by preventing potential hazards and accidents. Welding can strengthen weak or damaged rails, prevent rail buckling or warping due to temperature changes, and reduce the likelihood of derailment due to track misalignment or damage. This ultimately promotes a safer and more efficient working environment for crane operators and workers.
In conclusion, rail welding is an essential practice in the maintenance and operation of cranes. It can significantly enhance the crane's performance, durability, and safety, reducing the risk of accidents and downtime. When done properly, rail welding contributes to a more efficient and reliable crane operation, creating a positive impact on productivity and profitability.